Rubber lip seals are the most important element in the design of rotary shaft seals for decades. The radial lip seals are widely used in wet environments like ships, water pumps and tidal turbines. The lip seals keep the oil or grease lubricant inside the application and prevents the ingress of water and dirt.
HOW LIP SEALS WORK
Lip seals work with a small contact area on the liner, which in turn is placed around the shaft. The seal works due to a hydrodynamic lubricating film between the lip seal and its counter surface, this area is called the sealing gap and the film thickness in general is a few microns. The lubricating film is most stable between two flattened surfaces, therefore over time, the lip seals tip will slowly wear to a small sealing surface. This effect also occurs on the liner, where a wear track is formed to the shape of the sealing surface of the seal. The liner can be outfitted in stainless steel, with or without a Hard Metal Layer (HML). To make sure the lip seals stay in place, they are clamped in bronze or cast iron housing parts.
Our rotating shaft seals are build-up with NBR, FKM or FKM-EAL lip seals, Hastelloy® C4 springs, liners, gaskets, O-rings and housing parts like metal rings. All our sealing solutions for rotating equipment contain two up to five lip seals to ensure a reliable operation. The required number of double lip seals depends on the application and environment. Some to form a barrier against water ingress and another to prevent lubricant leakage into the environment.
THE FUNCTION OF LIP SEALS
To accomplish the desired sealing solution, a lubrication film and high-pressure compensation are the main functions of rubber lip seals.
LUBRICATION FILM
The lubrication film forms a barrier between two media, such as water and oil. Another advantage is that the lip seal and liner do not make contact. This results in less friction, therefore reduced energy consumption, less wear, longer lifetime and minimal heat development. Minimal heat development makes the lip seals very suitable for high-speed applications, where often increased heat results in aging of the lubricant.
PRESSURE COMPENSATION
The lip seals in high-pressure applications, e.g. centrifugal pumps, have an additional pressure reducing function. The rotary lip seals run over a partially grooved bush/liner which is placed over the shaft. The helical shape of the grooves and peripheral velocity of the liner creates water flow (similar to aquaplaning) between the grooves and the lip seal. It lubricates the lip seals with flush water, cools the module and minimises friction. The lip seals work with a controlled ‘leakage’ which is drained into a drain tank. Due to this special pressure compensation module, the lip seals can handle up to 40 bar of pressure.
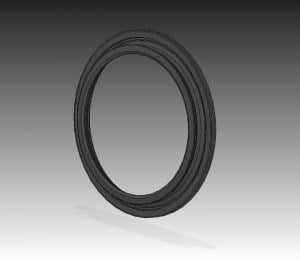
THREE MAIN FACTORS THAT AFFECT THE LIP SEALS
As seen in the image, there can be multiple factors that affect the sealing function of the lip seals. Spring force, liner condition, misalignment and film thickness could affect the lifetime and reliability for example. Despite the importance of previously mentioned factors, the main factors for the proper functioning of the lip seals are:
- Temperature
- Rubber compound
- Pressure differences
TEMPERATURE
The temperature could increase due to friction/load on the contact zone, more shaft rotations per minute (RPM) or pressure difference over the lip seal. A higher temperature could lead to heat cracks and blistering of the lip seals. This could affect the seals reliability and will inevitably lead to leakage.
When a lip seal operates in temperatures above the operating limit, it is likely that heat cracks will arise. Heat cracks are small axial cracks that are visible on the lip seal edge, caused by hardening of the compound. If the lip seal has hardened it is also possible for breakouts on the sealing edge to occur. Heat cracks and breakouts will inevitably lead to leakage.
With regard to the water-facing lip seals, another phenomenon can occur; water vapourises under heat. This vapour can enter the elastomer material and when the water condensates within the molecular structure of the elastomer blisters will be formed, affecting the sealing function of the lip seal. We have different rubber compounds suitable to ensure a long lifespan.
RUBBER COMPOUND SELECTION
The different elastomer rubber compounds each have their own operational temperature range, wear and chemical resistance. While NBR lip seals are more wear resistant, FKM lip seals are more chemical resistant and can endure higher temperatures. By calculating the PV value [bar × m/s] – pressure difference × velocity – Lagersmit can advise the proper lip seal compound for each Supreme seal. Higher PV values indicate a higher heat development, which in turn can influence the right choice of seal.
Where EALs are used, a large chemical resistance is wished. Therefore a special FKM-EAL lip seal compound is advised when EAL is used.
PRESSURE DIFFERENCE OVER THE LIP SEAL
The pressure difference over the lip seal is the difference between the fluid pressure distributed on the front of the lip seal and the fluid pressure that exists on the back of the lip seal. The greater the pressure difference, the greater the friction and temperature increase will be. If your vessel or pump has to deal with pressure drops or spikes, the wearing process will increase and possibly also the consumption of fluids.
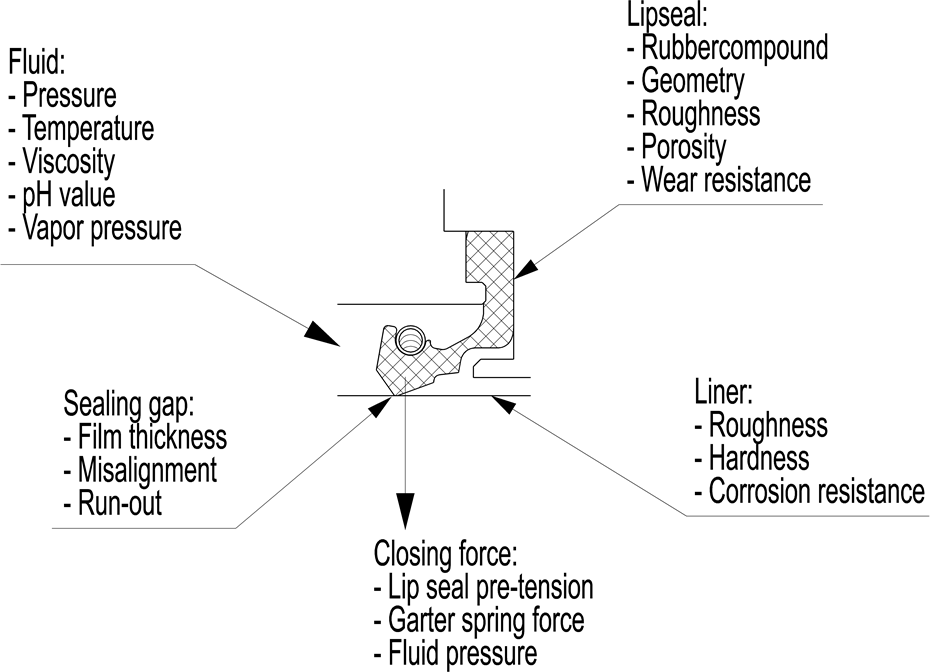